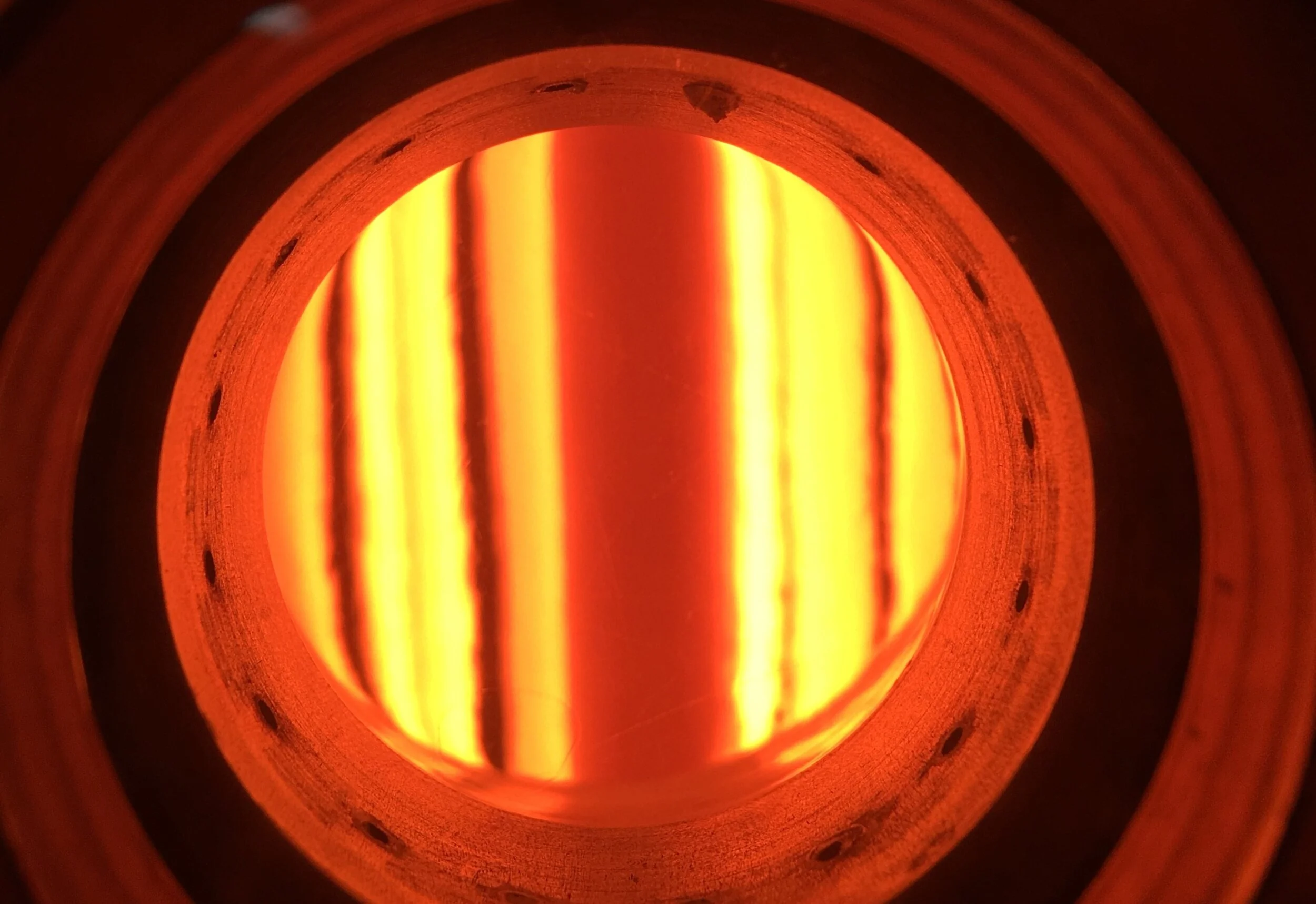
Polysilicon
Background
Polycrystalline silicon (polysilicon) is typically produced by reacting trichlorosilane and hydrogen in a bell jar style chemical vapor deposition (CVD) reactor. The CVD reactors run in a batch mode and contain silicon filaments that are resistively heated to over 1000°C. When the TCS contacts the hot filaments, it reacts and silicon deposits on the filaments. Throughout the run, the filaments grow into rods with diameters over 150mm. Many factors influence the time required for each batch, including the filaments’ initial surface area.
Depending on a polysilicon plant’s geographical location and the targeted final purity requirements, the bell jar’s internal surface can be made of stainless steel, silver, or a high nickel alloy. The materials of construction and detailed design of the reactor significantly impact the final polysilicon product quality. Choosing the wrong material or improperly designing cooling channels can lead to high reactor surface temperatures that will degrade the reactor’s surface and lead to lower quality polysilicon and higher energy usage. Reactors designed for photovoltaic grade polysilicon have to be retrofitted to make electronic grade polysicon.
In some instances, it is also desirable to put a reflective coating over an existing bell jar.
The preferred type of reflective material (for example, silver, gold or titanium nitride) depends on the design of the bell jar and local operating and investment costs. [Patents]
The reaction of trichlorosilane with hydrogen in a CVD reactor generates byproducts, including hydrogen chloride and numerous chlorosilane species. The byproducts are typically recycled for further use in the facility in the off-gas recovery (OGR) system but, in some cases, can be extracted and purified as saleable products.
For some special applications, such as the production of float zone grade polysilicon, monosilane can be decomposed in a CVD reactor to produce polysilicon.
Here is a video of highlighting AMS Polysilicon Solutions:
AMS Polysilicon Solutions
AMS experience/core competence in the area
AMS and its principals have designed more than five generations of CVD reactors, with hundreds of units in operation throughout the world. We have tested a wide range of materials and configurations, starting from simulations, then progressing the development into the laboratory, pilot plant scale and finally to the commercial process. AMS recommends that each producer adapt their CVD reactor based on optimizing cost and product performance for the specific plant site conditions and target market.
We have extensive experience in designing and operating silane and TCS reactors to produce Float Zone (FZ) grade polysilicon. These reactors require special design considerations to meet the FZ polysilicon requirements. AMS personnel have relevant customer references for designing reactors to meet current market requirements. [Patents]
AMS continues to push the envelope of technology to lower costs and improve product quality.
AMS product offering
AMS provides custom CVD technology solutions from the conceptual design through the pressure vessel and power supply component fabrication. We also provide operational support and continued optimization of the equipment and process. AMS offers the following equipment and technology:
CVD reactor for making CZ electronic grade polysilicon using TCS as the feed gas
CVD reactor for making FZ electronic grade polysilicon using silane or TCS as the feed gas
CVD reactor upgrades for modifying a PV grade reactor to make electronic grade polysilicon
Our business model is flexible to meet our customer requirements, such as directly providing technology equipment to produce tube filaments. Tube filaments increase productivity and reduce power consumption relative to traditional filaments.
Multi-tube Filament Puller
50mm Tube Filaments
Tube Filament in Puller
Polysilicon Grown Tube Filament